SNAP, CRACKLE, POP!
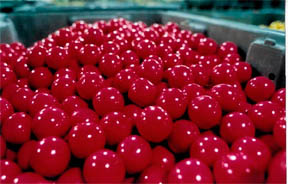
How Bubble Gum Balls Are Made
From Bubblemania: A Chewy History of Bubble Gum
by Lee Wardlaw, copyright 1997
All rights reserved
No part of the following may be used in any form
without permission from the author
Five Steps to Success
Mario D'Acri is Processing Supervisor at Leaf Canada, where the popular Rain-Blo Bubble Gum Balls are made. Today, D'Acri will be your tour guide. But before you can enter the manufacturing plant, you must take off any jewelry, put on a white lab coat, and tuck your hair into what looks like a shower cap.
Don't feel silly. All workers in the plant are dressed the same way. The company has strict rules and regulations about keeping the factory clean and sanitary. D'Acri says he doesn't want any stray hairs or earrings gumming up the works.
"Gumballs go through a five-step production process, which takes about three days from start to finish," D'Acri explains. He leads the way into a large room lined with rows of huge vats and kettles. Rectangular flats of hard gum base are stacked nearby. A sugary-sweet smell fills the air, tickling the back of your throat.
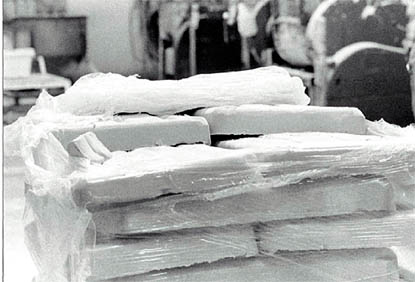
"Step one is called the Forming Process," D'Acri continues. "First, our workers break up the gum base into small pieces and heat it in these kettles. As the gum base heats, it melts, thickening like molasses or maple syrup. The syrup is then filtered to get rid of impurities and pumped into vats along with glucose, a sweetener. Glucose helps to keep the gum moist and easy to chew. Later, when we add powdered sugar, the glucose will also help it stick to the gum."
Each vat is equipped with giant blades that slowly revolve to mix the ingredients for about half an hour. (Some vats can mix two thousand pounds at a time.) The gum now resembles bread dough the color of ash.
As the blades knead the gum, powdered sugar is added, followed by softeners, such as glycerin or other vegetable oils. Softeners keep the gum moist and flexible for a good, springy chew. Finally, natural or artificial flavoring is added.
All the while, the giant blades keep turning. Already, the bubble gum is living up to its name: The twisting and churning action of the mixers causes bubbles the size of basketballs to form and pop.
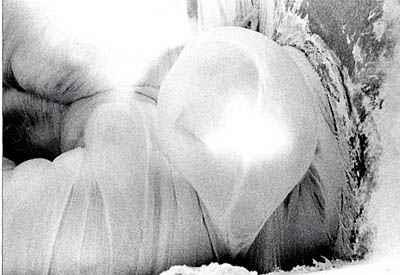
D'Acri now escorts you into a more spacious room. Conveyor belts criss-cross above your head.
After the gum is blended, he explains, it is then extruded or pushed through a machine the same way toothpaste is squeezed from a tube. This forms it into a smooth, continuous rope, similar to the “snakes” you may have made by rolling clay back and forth between your hands. Pencil-thin snakes become regular-sized gumballs. Thicker snakes become gargantuan balls, like jawbreakers.
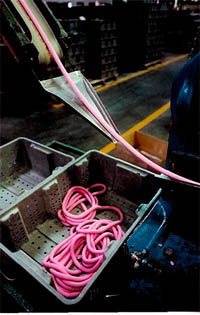
Whatever the size, the ropes of gum then travel along the conveyor belts into cooling tunnels, which surround the gum with cooled air to reduce its temperature. The conveyor belts and tunnels look like an elaborate amuse-ment park ride. Sort of a Disneyland for bubble gum!
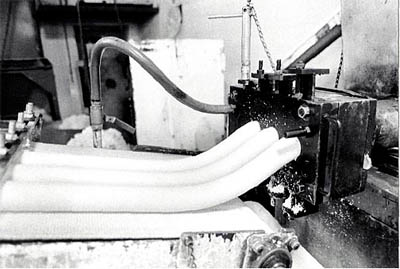
"The forming process is almost complete," D'Acri says. "Remember: not a single human hand ever touches the gum. Everything is done automatically, by machine."
You watch as special blades cut the ropes into measured segments. The segments continue their ride into a rolling machine that spins and twirls them on a large corkscrew-like mechanism. The twirling action forms them into perfectly rounded balls.
"When I was a boy," D'Acri confesses with a smile, "I used to think each and every gumball was formed by hand. If that were true, can you imagine how many workers we'd need? We make billions of bubble gum balls here every year!"
He plucks one off the conveyor belt and offers it to you. You shake your head. The gum is still gray and unappetizing. You decide to wait and see what happens during the next step of production.
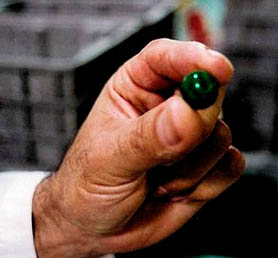
Wow . . . Gross!
While in the rolling machine, the gumballs have heated up again. Now they must travel through another cooling tunnel. The tunnel rumbles like minor earth-quake, shaking gently back and forth to keep the texture and shape of the balls uniform. Any that get flattened on one side are rejected and thrown away.
"This is the grossing process," states D'Acri. "The gumballs tumble through one last tunnel, and roll out into plastic crates. Workers stack these crates in our storage facility, which is climate-controlled. The temperature in there is about 64 degrees Fahrenheit. The gum will remain at that cool temperature for 24 hours, until the balls harden enough to coat."
The gum will also be tested by quality control technicians. These specialists inspect ingredients and conditions daily to make sure the gum is of the highest quality.
The Finishing Line
Your guide continues the tour. As you approach the next room, it starts to sound like rocks crashing down in an avalanche. Curious, you cover your ears (the noise hurts!) and walk inside.
"This is the Finishing Room," D’Acri shouts over the din.
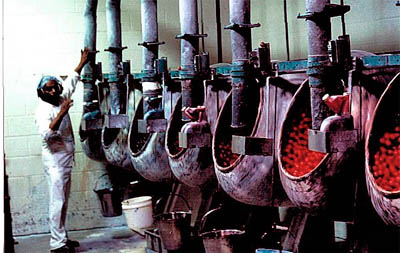
You glance around. Each long wall of the room is lined with giant pot-bellied kettles, their wide mouths gaping at you. The kettles are filled with gumballs in red, orange, blue, green, pink, yellow, and white. They rotate, tumbling the balls over and over like laundry in a clothes dryer. But unlike socks and T-shirts, these hard balls produce ear-splitting sounds as they roll against each other. You watch for a few more minutes, breathing in the sweet fruity scent that surrounds you. Finally, the noise drives you back into the other room.
D'Acri chuckles as you massage your ears. "Our workers in the Finishing Room must wear special headphones to block out the noise," he says. “They are similar to what ground crews wear at airports to protect their ears from the deafening jet roar."
But what exactly happens in the Finishing Room?
"After the grossing process," explains D'Acri, "workers scoop about 300 pounds of balls into each of those tumbling kettles. Then powdered dextrose is ladled in, along with color and liquid flavoring. The tumbling action makes sure each gumball is coated evenly. It also helps to remove moisture. This procedure takes about one hour and twenty minutes, including loading and unloading the kettles.”

D'Acri guides you toward the next room, which is just as noisy as the previous one. "When the finishing process is done, then we begin the glazing. Once again, the gumballs are scooped into kettles and tumbled. When the final coat of liquid color is ladled in, the tumbling
motion polishes the gum, which produces a glazed or glossy look. Beeswax is also added to give the gum extra shine."
The two of you move away and pass a long conveyor belt with rollers. "Some of our gum has writing or designs on it," D'Acri says. "That gum goes through our Branding Department. Each of these rollers is etched with printed words or an illustration. It picks up edible, quick-drying ink, and rolls the design onto the balls as they pass under. If the gum has no design, then it goes directly from the Glazing Process to the final step: packaging."
Good Things Come in Small Packages
The tour of Leaf's gumball factory is coming to a close.
"The gumballs travel along this next set of conveyor belts into the packaging machine," D'Acri explains. "The machine automatically wraps the gum in plastic and seals it with heat.” (Some gum-wrapping machines have up to 16,000 moving parts!) “Technicians oversee the process to make sure everything runs smoothly. Then they load the individually wrapped pieces of gum into boxes or plastic bags, which are sealed airtight and marked with a quality assurance date. The gum is then packed into shipping cases, and sent to hundreds of thousands of stores all over the world."

D'Acri motions you toward a stairway. “Let me show you something."
You follow him up the stairs. You find yourself on a catwalk, high above the factory.
You look down and suck in your breath.
Below, stands crate after crate, brimming with a rainbow of gumballs, all glossy and glowing under the bright lights of the factory. The crates are stacked almost head-high, in rows that stretch far as you can see.
"And that's just one-and-a-half day's worth of gum," D'Acri says.
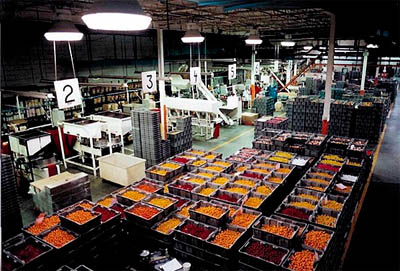
You let out your breath in a low whistle.
Your guide leads you back downstairs, then out into the bright sunshine. You thank him for taking the time to show you around.
"You're welcome," he says, and hands you a large, sealed box. "Oh, and here's a little souvenir of your tour. Something to remember us by.”
You wave and walk away. You don't open the box. You don't need to. Inside you know what you'll find: Enough bubble gumballs to make any kid happy.
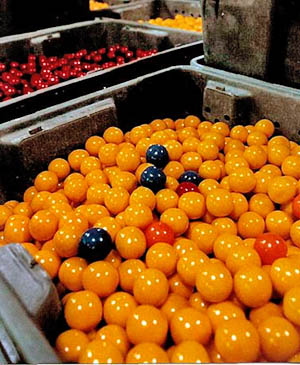